A new era of intralogistics flexibility
4th November 2022
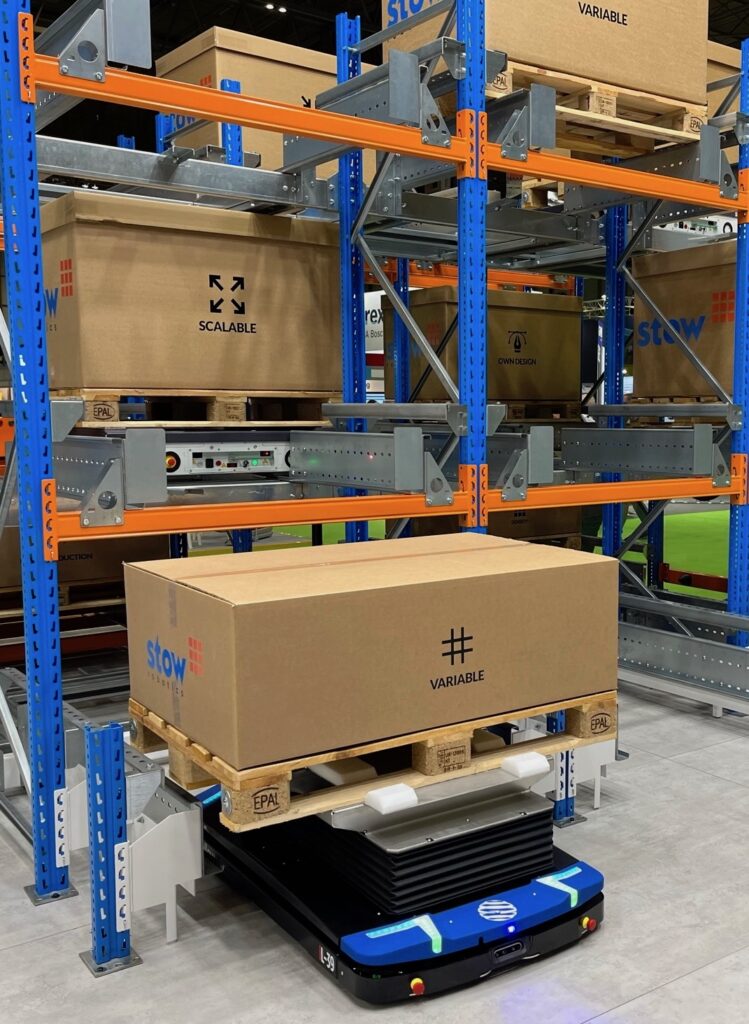
Frazer Watson, VP-Sales UK/Ireland at Autonomous Mobile Robots (AMR) designer and manufacturer iFollow, explains how mobile robots offer agile organisations the flexibility required to come through unpredictable times with an advantage over the competition.
We have entered a new era of intralogistics, one were flexibility is paramount, giving companies the agility they need to deal with whatever the near-future has to throw at us. Given the experience of the last few years, this can be a lot.
When storm winds blow hard, the trees able to bend with it are the ones that survive. Similarly logistics operations that can flex in times of turbulence or rapid trend switches will be better placed to ensure continuity of service, whatever happens. They must also put themselves in a position where they have a competitive edge when upswings occur rather than struggling to meet demand.
Striving for efficiency and productivity in storage and order picking in the past has seen many go down the road of solutions incorporating Automated Storage and Retrieval Systems (ASRS) and conveyors. Such solutions provide dense storage and rapid order picking, giving sufficient productivity to go someway to recouping the considerable investment they demand. However, when business circumstances change, it soon becomes apparent how rooted to the floor this type of materials handling equipment can be.
There is a broad scale when it comes to adapting a warehouse to meet change – from rearranging SKU locations according to seasonal demand, right up to complete refits. It is certainly true in the later case that modifying a facility amid the mass of steel involved in an ASRS and obstructive runs of conveyors can be tricky at best.
Today, thanks to Autonomous Mobile Robots (AMRs), warehouses can benefit from the advantages of automation without the need to bolt materials handling equipment to the floor. AMRs adapt easily to any constraints presented by current installations. If the building is new and/or empty, then a fresh AMR system installation makes life even easier. Providing an automated materials handling solution without the need for dedicated infrastructure allows a building to become operational more quickly than would be the case with a ‘traditional’ automated installation.
Equipped for autonomous navigation, AMRs offer a level of safety far superior to human handling. Their security cameras and LIDARs (Light Detection and Ranging) allow them to travel on complex routes that are much narrower than AGVs and have a perfect perception of the environment. The robot analyses the situation in real time in order to avoid obstacles or even overtake slower vehicles. This is achieved through wide-angle stereoscopic camera and long distance LIDAR.
AMRs equipped with two 3D-cameras both front and rear, gain from a three-dimensional perception with a wide viewing angle and volumetric detection of objects even at long distances. Perceiving the environment, safety LIDARs complementing each other will play an essential role in the 360° object detection of the vehicle.
Navigation modes take into account the proximity of the user, for example during order preparation. The faster the robot moves in one direction, the more the viewing area stretches. Likewise, the area changes shape depending on the type of object transported. If an obstacle enters the robot area then its emergency stop is instantly triggered. With this technology in place, secure cohabitation between AMR and operators, whatever is being transported, is assured, giving warehouses the flexibility for AMRs to work safely and productively in collaboration with people.
Flexibility is also facilitated by AMRs in terms of the approach a company adopts for automating a warehouse. Mobile robots offer a scaleable solution, allowing operations to start with one unit and build up a fleet as required, or units can be switched with different capacity models. When business levels reduce, units can be removed, thus eliminating redundant operation and allowing the warehouse to operate only the powered equipment it actually needs.
Being able to perform a broad variety of tasks is a further feather in the cap for AMRs. Providing internal transport to support order picking is often a key role, allowing staff to remain in the pick zones where they are most productive rather than simply pushing a roll cage or pallet truck from the picking aisles to the packing or marshalling areas. They can also be used to transport returned items – anything that reduces the time and effort required to process returns will contribute to regaining maximum value from the return. Mobile robots can handle a variety of load units from cases and pallets to trolleys and roll cages.
iFollow AMRs stand apart by being able to carry two roll cages at once to a total load of 1,500kg. Potentially, on a single pick walk an operator attended by two AMRs could be assembling orders for four different stores or customers. In practice, improvements in overall operational productivity of between 28% and 42.5% are routinely reported. This ability is particularly useful for grocery logistics. An ability to comfortably perform in temperatures from -25° C to +40°C without degradation of battery life suits coldstores seeking ways to minimise energy use. This will give logistics operations, including those in the grocery sector, much appreciated flexibility in being able to work across ambient and cold areas.
All of the flexibility delivered by AMRs is within reach of SMEs as falling costs for the technology combines with a growing list of good reasons to make that investment, such as: changing workforce demographics, constraints on supply and movement of goods, supply chain disruption, meeting the demands of online retail and the ever continuing drive to improve productivity. Don’t get left behind, it’s time to join the new era of flexible intralogistics now.